views
Understanding the Role of Gearboxes in Industrial Applications
Common gearbox types and their uses
Industrial gearboxes maintenance serve as the backbone of mechanical power transmission across multiple sectors. From helical and bevel gearboxes used in steel production to planetary and worm configurations in automated assembly systems, each type performs a specific role under varying loads and environments. The choice of gearbox often depends on torque requirements, spatial constraints, and operational cycles.
Each configuration offers a unique balance of strength, efficiency, and precision. Bevel helical units, for instance, are ideal for continuous heavy-duty use, while worm gearboxes are valued for their quiet operation and ability to handle shock loads. When aligned with the correct application, gearboxes contribute significantly to productivity and system longevity.
Why performance consistency matters
Reliable gearbox operation is essential for maintaining output in manufacturing and processing environments. Any inconsistency in performance—whether in speed, torque, or directional control—can disrupt entire production lines. These systems are not just mechanical components; they represent critical links in energy transmission that affect downstream operations.
Beyond output concerns, inconsistent gearbox behaviour can also cause stress on connected machinery. This leads to premature wear, reduced efficiency, and potentially expensive secondary failures. Proactive maintenance and awareness of gearbox behaviour ensure smoother operations and reduced risk across the board.
Signs of gearbox strain or degradation
Over time, gearboxes naturally experience wear, but there are early indicators that signal deeper issues. Unusual vibrations, changes in noise patterns, or temperature spikes may suggest alignment problems, bearing damage, or gear tooth wear. Monitoring these signs can help identify minor issues before they escalate.
A drop in performance efficiency or irregular power delivery may also suggest internal degradation. Oil contamination, misaligned shafts, or deteriorating seals can accelerate the decline. Timely diagnosis and intervention are essential to avoid costly unplanned downtime and to maintain system integrity.
What Regular Gearbox Maintenance Involves
Visual inspections and wear tracking
Routine visual checks remain a foundational part of gearbox servicing. Inspectors typically look for leaks, discolouration, loose fixings, or debris accumulation around critical seals and junctions. While simple, these checks often reveal early-stage problems that could lead to more serious mechanical faults.
Tracking wear on components such as gears, bearings, and shafts helps assess the unit’s condition over time. Comparing measurements against original specifications enables engineers to identify patterns and intervene before tolerances exceed safe operational limits.
Lubrication standards and schedules
Maintaining correct lubrication is essential for minimising friction and preventing overheating. Each gearbox type has a specific lubricant requirement, depending on load, speed, and ambient temperature. Using the wrong oil—or neglecting scheduled changes—can result in rapid internal damage.
Service schedules should include lubricant analysis to check for contamination, metal particles, and degradation. Periodic sampling helps determine whether a change is needed and identifies signs of premature wear. Staying ahead of lubrication issues is one of the most cost-effective ways to extend gearbox life.
Noise, vibration, and heat monitoring
Changes in noise levels often indicate internal misalignment or damaged gears. Unusual humming, knocking, or whining sounds are not just irritants—they are diagnostic clues. Capturing audio signatures and comparing them with baseline readings can aid early fault detection.
Vibration analysis and thermal imaging further refine the diagnosis. Persistent vibrations may signal unbalanced shafts or failing bearings, while hotspots can highlight overloaded components. These tools provide a non-invasive way to monitor gearbox health and refine maintenance plans based on real data.
Digital diagnostics and performance analytics
Modern gearboxes benefit from integrated sensors and digital monitoring tools. These systems record data such as torque fluctuations, lubricant levels, and thermal conditions in real time. The insights allow maintenance teams to plan service intervals more accurately and respond to issues as they develop.
Remote diagnostics also support multi-site operations, providing consistent oversight without the need for on-site technicians. By analysing trends across usage cycles, businesses can align maintenance planning with production goals, increasing uptime and reducing reactive service calls.
Long-Term Benefits of Routine Servicing
Avoiding unplanned downtime
Unexpected gearbox failure can halt entire production lines, creating logistical challenges and financial losses. Routine servicing plays a critical role in preventing such scenarios by identifying worn parts, insufficient lubrication, or alignment issues before they escalate.
By adopting a proactive maintenance schedule, businesses reduce reliance on emergency repairs. This approach not only supports consistent output but also enables teams to plan servicing around production cycles, avoiding disruption and maintaining delivery commitments.
Extending gearbox lifespan
A well-maintained gearbox can outlast its expected operational life. Regular servicing reduces stress on critical components, allowing them to function optimally for longer periods. Replacing consumables such as seals, bearings, and lubricants at the right time helps avoid secondary damage to more expensive internal parts.
Servicing also enables condition-based planning. Instead of replacing gearboxes on fixed timelines, teams can assess wear and performance data to make informed decisions. This results in better resource use, improved cost control, and greater return on investment.
Maintaining energy efficiency
Friction, misalignment, and wear all increase the energy required to drive a gearbox. Over time, this inefficiency compounds, pushing up operational costs. Proper maintenance restores optimal mechanical contact, improving power transmission and reducing energy loss.
Servicing also ensures that internal clearances remain within spec. Gear teeth that are too loose or too tight affect load distribution, generating unnecessary resistance. Maintaining correct tolerances keeps performance sharp and helps meet energy efficiency targets.
Reducing total cost of ownership
The upfront cost of gearbox maintenance may seem high, but it is far less than the cumulative cost of failure, unplanned repairs, and productivity loss. Scheduled servicing extends equipment life and delays capital expenditure on replacements.
Moreover, a structured maintenance regime builds operational resilience. It reduces the risk of secondary equipment damage caused by gearbox failure, which can drive costs higher and complicate insurance claims. Over time, a preventive approach pays off in both reliability and financial performance.
Gearbox Refurbishment: When Repairs Aren’t Enough
Difference between repair and refurbishment
Repairing a gearbox usually involves replacing faulty components and restoring basic function. Refurbishment, on the other hand, is more comprehensive. It includes complete disassembly, deep cleaning, inspection, re-machining where needed, and the replacement of worn or obsolete parts.
Refurbishment restores the gearbox to near-original condition. This process is especially valuable when sourcing a new unit is costly or time-consuming. It combines the benefits of new performance standards with the savings and environmental gains of reusing existing infrastructure.
Indicators refurbishment may be necessary
Gearboxes that experience repeated breakdowns or show excessive wear across multiple parts often benefit more from refurbishment than piecemeal repairs. Frequent oil leaks, severe noise, or visible structural damage suggest deeper issues that single-point fixes won’t resolve.
Refurbishment is also suitable for ageing gearboxes with outdated parts. When manufacturers no longer supply original components, rebuilding the unit to modern specifications can restore function and enhance reliability. This option avoids full replacement and keeps legacy systems running effectively.
Key steps in the refurbishment process
The process begins with complete disassembly and assessment of every component. Engineers inspect gear teeth, shafts, bearings, and housings for cracks, wear, or fatigue. Damaged parts are replaced or remanufactured using CNC machining to meet original tolerances.
Once parts are restored or replaced, the gearbox is reassembled under clean-room conditions. This ensures no contaminants affect the build. The refurbished unit is then tested under load, with vibration, noise, and temperature measurements confirming performance before it’s approved for return to service.
Impact on lead time and performance
Refurbishment often delivers faster turnaround times than sourcing new gearboxes, particularly for specialist or obsolete models. By relying on in-house expertise and modern machining techniques, service providers can reduce delays and eliminate dependence on external suppliers.
Performance gains from refurbishment can rival or exceed those of a new unit. Upgraded seals, modern lubricants, and precise reassembly often improve durability and efficiency. Businesses benefit from renewed reliability without committing to the cost of full replacement.
Working with a Specialist Service Provider
Why in-house capability matters
Choosing a service provider with in-house capability allows for greater control over quality, lead time, and accountability. When gearbox refurbishment or repair is carried out under one roof, communication gaps are reduced, and technical teams can collaborate directly on problem-solving.
In-house machining and diagnostics also eliminate delays caused by outsourcing. Service continuity improves because engineers familiar with the original issue oversee the entire repair or refurbishment process. This consistency helps ensure higher accuracy, reliability, and quicker turnaround.
Evaluating technical expertise and experience
Not all gearbox servicing partners are equal. Experience with a wide range of gearbox types—such as planetary, bevel helical, and worm designs—demonstrates versatility and understanding of diverse industrial applications. Providers who specialise in competitor gearboxes like Flender, DB Santasalo, or Hansen can offer added assurance.
A proven track record should be backed by technical accreditations, advanced tools, and a clear understanding of both mechanical and operational considerations. These elements indicate a provider’s ability to meet rigorous standards and adapt to industry-specific demands.
Typical turnaround times and service scope
Turnaround time can vary significantly depending on the gearbox type, complexity of work, and availability of replacement parts. However, a competent service provider should offer transparent timelines and the ability to respond quickly in critical situations.
The service scope should go beyond basic repairs. Comprehensive providers assess associated components, align systems, and offer performance testing post-repair. Their goal is not just to restore function but to return the gearbox in a condition that maximises uptime and minimises risk.
Case examples from heavy-duty industries
In steel production, high-load bevel gearboxes face constant stress. A refurbishment project involving CNC-machined components and upgraded bearings extended one unit’s operational lifespan by five years—avoiding the six-month lead time for a replacement. That result stemmed from having in-house expertise and rapid response capability.
Similarly, a beverage manufacturing plant saw significant benefits after switching to a specialist for scheduled gearbox audits. Reduced vibration, better lubricant retention, and zero unexpected failures over 12 months confirmed that skilled servicing can directly impact bottom-line performance.
Preventive Strategies for Gearbox Health
Scheduled audits and predictive maintenance
Routine audits are the cornerstone of preventive care. By tracking vibration, heat signatures, and load patterns, engineers can build a clear profile of gearbox health. This data supports predictive servicing—repairs are made before components fail, not after.
Predictive maintenance allows teams to schedule interventions during planned production breaks. This approach prevents unplanned downtime and protects supporting equipment from secondary damage, ultimately saving both time and cost over the machine’s lifecycle.
Importance of environment and operating conditions
Operating conditions play a significant role in gearbox wear. High temperatures, dust, moisture, or corrosive chemicals can degrade seals, lubricants, and internal components faster than expected. Understanding these factors is critical when developing a maintenance plan.
Environmental factors should inform servicing intervals and inspection frequency. For example, gearboxes in high-humidity environments may require more frequent checks for water ingress, while units operating near furnaces might need specialised heat-resistant lubricants and seals.
Choosing the right lubricants and components
Not all lubricants offer the same level of protection. Gearboxes require oils that match their load type, temperature range, and duty cycle. Selecting high-performance or synthetic oils where needed helps preserve internal surfaces and maintain efficiency.
Similarly, component choice affects service life. Bearings, seals, and gears manufactured with superior materials or tighter tolerances often perform better under stress. A knowledgeable provider will always match parts to application demands, rather than defaulting to the cheapest option.
Role of CNC machining in precise component restoration
CNC machining enables component restoration with exceptional precision. Damaged shafts, gears, or housings can be re-machined to original specifications or improved where design flaws existed. This process ensures that replacement parts are dimensionally perfect, maintaining gearbox performance and balance.
Using CNC machining also improves repeatability and traceability. Once a component is programmed into the system, it can be replicated quickly for future refurbishments. This capability supports fast, reliable service, especially for rare or discontinued gearbox models.
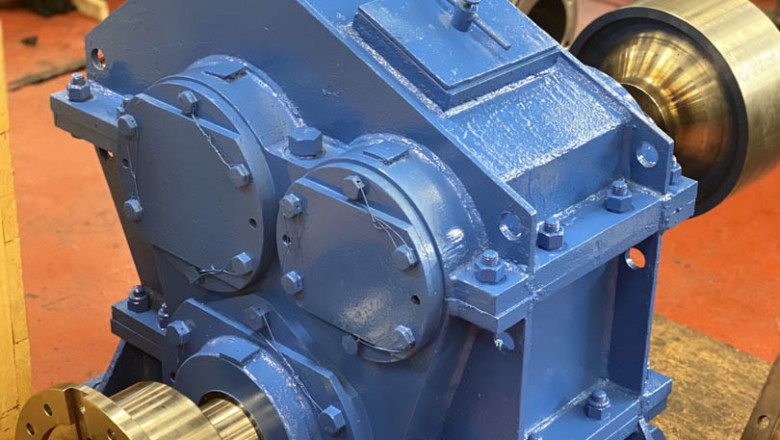

Comments
0 comment