views
As you consider electronics manufacturing service or EMS, it's simple to envision assembly lines, components tidily soldered onto circuit boards, and finished products waiting to be shipped. While creating physical electronics is at the core of their function, EMS providers do so much more than production. Their skill and ability reach into design, testing, logistics, and after-sales service, and thus they are an invaluable partner to companies in a wide range of industries.
If you are wondering how EMS providers create value above and beyond production, this article is for you.
Electronics Manufacturing Service Go Beyond the Factory Floor
The EMS industry of today functions at the interface of technology, innovation, and efficiency. Here's how these services go well beyond the nuts and bolts of assembly.
1. Product Design and Development Expertise
Prior to manufacturing a product, the product must be designed - an activity in which most EMS providers do very well. EMS firms typically have talented engineering teams that work together with customers to create efficient, scalable, and cost-effective designs.
This stage may incorporate services such as:
•Design for Manufacturing (DFM): Refining product designs so that they're simple to manufacture with reduced costs and errors.
•Prototyping, prototyping: Developing product prototypes to confirm designs, investigate functionality, and check feasibility prior to large-scale production.
•Innovation Support: Providing ideas for improved materials, components, or designs to enhance product functionality or lower manufacturing overheads.
2. Testing and Quality Assurance
Reliability is critical for electronics, and EMS providers appreciate this more than anyone else. Quality testing and assurance services form an integral part of their solutions, with the goal of every product meeting tough functional and safety standards before release into the marketplace.
Test capability typically encompasses methodologies such as:
•Automated Optical Inspection (AOI): Confirmation of the accuracy and positioning of components on a circuit board.
•Functional Testing: Imitating product usage to ensure that the product functions as desired.
•Environmental Testing: Testing a product's capability to sustain factors like temperature fluctuations, humidity, and vibration.
A strong emphasis on quality at this point decreases the risk of failure or recalls, assisting companies in gaining solid reputations and customer trust.
3. Supply Chain Management Support
EMS providers are crucial stakeholders in supply chain management to facilitate seamless and unbroken processes, even across intricate global networks.
Responsibilities in this field are:
•Component Sourcing: Utilizing relations with suppliers to source quality components at competitive prices while avoiding delay due to shortages.
•Inventory Management: Optimizing inventory processes to avoid waste or delays while preserving the continuity of production.
•Logistics Optimization: Scheduling global shipping and deliveries to get finished goods to destinations in an efficient manner.
From managing disruption due to supply chain disruptions or requiring materials sourced ethically, EMS providers offer flexibility and vision.
4. Scalability to Meet Demand
The other essential aspect of EMS providers is their capacity to quickly ramp up production to keep pace with shifting demand. Startups and existing companies both appreciate the flexibility of EMS partners, who can increase (or decrease) production based on market demand, seasonal fluctuations, or new product launches.
By ramping up production, EMS providers enable companies to remain agile without incurring heavy capital expenditures on equipment or staffing.
5. Lifecycle Management and Aftermarket Services
EMS alliances do not cease upon production exit from the factory floor. Several providers provide assistance with continuing product lifecycle management to maximize customer satisfaction and loyalty.
Aftermarket services may include:
•Repair and Refurbishment: Facilitating continued product utilization by repairing or refurbishing electronics for consumers.
•Spare Parts Management: Inventorying spare parts to maintain products well after first sale.
•Recycling and Disposal Services: Providing eco-friendly solutions to recycle electronic parts and support a circular economy.
6. Compliance and Regulatory Support
It can be challenging for companies to navigate the world of electronics manufacturing regulations. EMS providers tend to have staff responsible for ensuring international compliance with standards and certifications.
This involves:
•Compliance with environmental regulations like RoHS (Restriction of Hazardous Substances).
•Compliance with industry-specific certifications, either for medical devices, automotive electronics, or consumer goods.
•Regular audits to maintain ethical employment practices and sustainability objectives.
By managing compliance needs, EMS companies enable businesses to circumvent expensive fines as well as improve the credibility of their market presence.
7. Cost Efficiency through End-to-End Solutions
The integration of all these EMS services results in unrivaled cost-effectiveness for businesses. Using end-to-end solutions, firms minimize time wasted communicating with a series of providers and erases communication misprints among various parties.
EMS service providers have the expertise of overseeing every aspect of the process - design through delivery - so there is quick turnaround and less in overall costs to clients.
Conclusion
Electronics manufacturing service or EMS companies are not mere suppliers but strategic partners. They possess the design, test, supply chain, and lifecycle management expertise to enable companies to concentrate on innovation while entrusting manufacturing complexities to capable hands.
Whether you are a startup launching your first product or a large company scaling up around the world, selecting the appropriate EMS partner can make all the difference for efficiency, quality, and competitiveness.
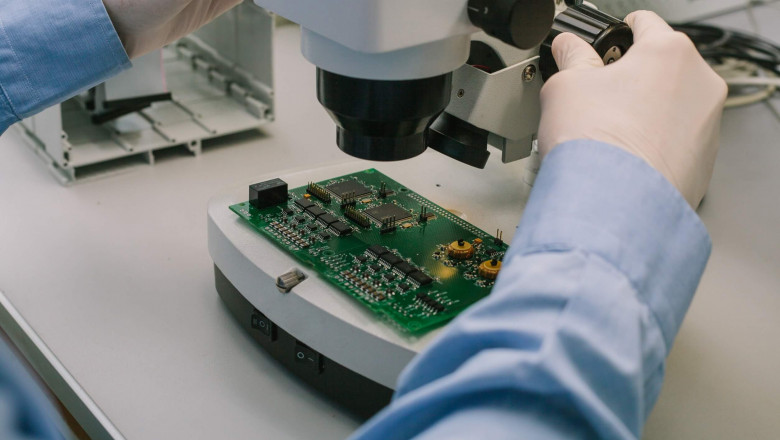

Comments
0 comment