views
ACSR Conductor is a type of high-capacity, high-strength stranded conductor used in overhead power lines. It combines lightweight aluminum strands with a strong steel core, providing an optimal balance of conductivity and tensile strength.
This unique structure makes ACSR the preferred choice for utility companies and grid developers around the world—especially in long-distance, high-voltage power transmission.
ACSR Conductor Construction
Component | Material | Function |
---|---|---|
Outer Strands | Aluminum (1350-H19) | High conductivity and corrosion resistance |
Central Core | Galvanized Steel | Mechanical strength, supports tension loads |
The number of aluminum and steel strands varies depending on the type and specification, impacting strength, weight, and electrical performance.
Why ACSR Conductor is Crucial in Power Transmission
-
High Strength-to-Weight Ratio: Ensures longer spans with fewer support structures.
-
Excellent Conductivity: Aluminum ensures minimal energy loss during transmission.
-
Corrosion Resistance: Essential for extreme weather and coastal installations.
-
Cost-Effective: Steel reinforcement reduces sag and requires fewer towers.
Common ACSR Conductor Types and Specifications
ACSR Type | Stranding (Al/Steel) | Overall Diameter (mm) | Approx. Weight (kg/km) | Rated Strength (kN) |
---|---|---|---|---|
Drake | 26/7 | 28.14 | 1125 | 61.5 |
Linnet | 26/7 | 18.14 | 570 | 31.5 |
Dove | 26/7 | 21.00 | 710 | 38.2 |
Zebra | 54/7 | 28.62 | 1221 | 63.1 |
Moose | 54/7 | 31.77 | 1416 | 71.2 |
Note: Specifications can vary by region and manufacturer standards.
Applications of ACSR Conductors
-
Overhead Transmission Lines: Most common use, especially for long distances.
-
Distribution Grids: In medium and high-voltage rural power supply networks.
-
River and Valley Crossings: Where long spans are needed.
-
Interconnectors: Used in national and international grid connections.
ACSR vs AAC vs AAAC – What's the Difference?
Feature | ACSR | AAC (All Aluminum Conductor) | AAAC (All Aluminum Alloy Conductor) |
---|---|---|---|
Strength | Very High (Steel Core) | Low | Moderate |
Conductivity | High | Very High | High |
Corrosion Resistance | Good (with Galvanized Steel) | Excellent | Excellent |
Weight | Moderate | Light | Light |
Span Length | Long | Short | Medium |
Best Used For | Long Distance, Harsh Conditions | Short Spans, Urban Areas | Coastal and High-Corrosion Zones |
Key Standards Governing ACSR Conductor Manufacturing
-
ASTM B232/B232M – Standard for ACSR conductors in North America
-
BS 215 Part 2 – British Standard for ACSR specifications
-
IEC 61089 – International standard for conductors
-
IS 398 Part II – Indian Standard for ACSR conductors
Benefits of Using ACSR in Power Infrastructure
🔹 Long Lifespan
Built to last decades under harsh weather, mechanical stress, and pollution.
🔹 Minimal Line Losses
High aluminum purity ensures excellent electrical performance.
🔹 Reduced Infrastructure Costs
Stronger spans reduce the number of towers needed in installations.
🔹 Thermal Stability
Can operate under high thermal loads (up to 85°C and beyond in emergencies).
🔹 Versatility
Suitable for use in flat terrain, mountainous regions, and even in salty coastal air.
Maintenance and Inspection Guidelines
Proper installation and regular maintenance of ACSR conductors are key to longevity.
Routine Checks Should Include:
-
Sag-Tension Evaluation
-
Corrosion Inspection (especially at joints and supports)
-
Thermal Imaging to identify hotspots
-
Vibration Dampers to prevent Aeolian vibration in windy zones
How to Choose the Right ACSR Conductor
When selecting an ACSR conductor, consider the following:
-
Voltage Level & Current Requirement
-
Geographical Terrain
-
Environmental Conditions (humidity, salt, etc.)
-
Span Distance Between Towers
-
Budget Constraints
Pro Tip: Engineers often run simulations using software like PLS-CADD to optimize conductor selection for mechanical and electrical performance.
FAQs About ACSR Conductor
Q1: What is the maximum temperature an ACSR conductor can withstand?
A: Standard ACSR conductors can operate continuously up to 85°C. High-temperature variants (HTLS) can go beyond 150°C.
Q2: Can ACSR be used in coastal environments?
A: Yes, but galvanized steel cores may be upgraded to zinc-aluminum coated steel for improved corrosion resistance.
Q3: How do I calculate the ampacity of an ACSR conductor?
A: Ampacity depends on conductor size, ambient temperature, wind speed, and solar radiation. Utility engineers use thermal calculation models to determine this. Typical ampacity for a Drake ACSR is about 700–800 A under normal conditions.
Q4: Is there a risk of galvanic corrosion in ACSR?
A: While steel and aluminum are dissimilar metals, galvanization and proper design minimize galvanic corrosion. Regular inspection helps catch early signs.
Q5: What’s the difference between “greased” and “non-greased” ACSR?
A: Greased ACSR conductors have anti-corrosive grease applied between strands to enhance lifespan in aggressive environments.
Installation Best Practices
-
Use hydraulic compression joints and dead-end clamps.
-
Avoid bending the conductor below its minimum bending radius.
-
Ensure the tension applied during stringing matches design specs.
-
Always use proper PPE and follow regional electrical safety regulations.
Key Takeaways at a Glance
🔧 Material: Aluminum (conductor), Steel (reinforcement)
⚡ Purpose: High-voltage overhead power transmission
📈 Strength: High tensile load-bearing for long spans
🛠️ Use Cases: Utility lines, rural grids, interconnections
🧪 Standards: ASTM, BS, IEC, IS
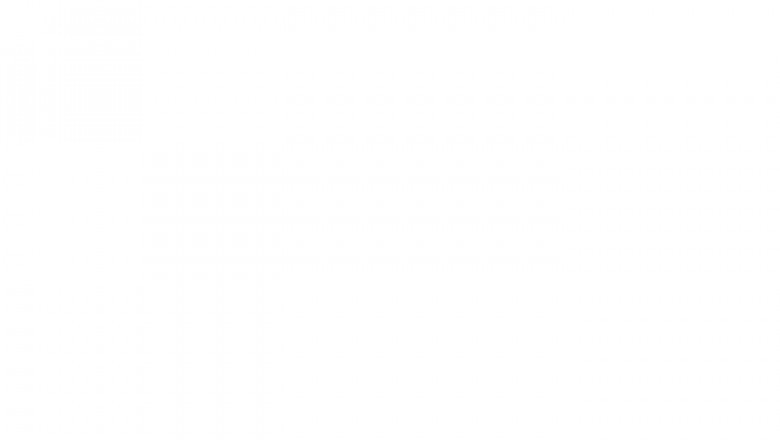

Comments
0 comment