views
In the world of electronics, precision is paramount. Whether you're working with sensors, circuit boards, or other intricate devices, the need for accurate resistance values is critical. One advanced technique used to achieve this precision is resistor trimming laser technology. This method allows for the fine-tuning of resistor values, ensuring optimal performance in a wide range of applications.
Understanding Thick and Thin Film Resistors
Before diving into resistor trimming lasers, it’s essential to understand the difference between thick and thin film resistors. Both are common types of resistors used in various electronic circuits, but they differ in their construction and application.
-
Thick Film Resistors: Thick film resistors are created by depositing a thick layer of resistive material onto a ceramic substrate. This material is often a metal oxide or a similar compound, and its thickness allows for a greater range of resistance values. These resistors are typically used in high-power applications where durability is crucial.
-
Thin Film Resistors: On the other hand, thin film resistors are made by depositing a much thinner layer of resistive material onto a substrate, often using vacuum deposition. This thinner layer results in higher precision and stability, making thin film resistors ideal for applications where accuracy is essential, such as in precision instrumentation and sensitive electronics.
The Role of Resistor Trimming Lasers
Now, let's focus on resistor trimming laser technology, a cutting-edge method used to modify the resistance value of both thick and thin film resistors. Laser trimming works by precisely removing a small amount of the resistive material on the resistor, thereby altering its resistance.
For thick film resistors, the trimming process can be more robust, as the thicker material allows for more significant adjustments. This method is often used for high-power applications where a small variance in resistance can have a substantial impact on overall performance.
In contrast, thin film resistors require more delicate adjustments. The laser trimming technique allows for finer changes, enabling the resistor to meet exact resistance specifications even in the most precise applications. By using a laser, manufacturers can achieve highly accurate resistances without compromising the integrity of the resistor.
Advantages of Laser Trimming for Resistors
The use of laser trimming provides several advantages over traditional trimming methods, such as mechanical trimming:
-
Precision: Laser trimming offers unmatched precision, especially when working with thin film resistors. The process is highly controlled, ensuring that each resistor meets exact specifications.
-
Non-contact: Unlike mechanical trimming methods, laser trimming is non-contact, meaning that there is no risk of damaging the resistor during the process.
-
Speed: Laser trimming is fast and efficient, allowing for rapid production of high-quality resistors.
-
Flexibility: The laser trimming process can be applied to both thick and thin film resistors, making it versatile for a wide range of applications.
Thick Film vs. Thin Film: Choosing the Right Resistor
When deciding between thick and thin film resistors, it's important to consider the specific requirements of your application. Thick film resistors are ideal for high-power environments where size and precision are less critical, while thin film resistors are perfect for applications demanding precision and stability.
The laser trimming process ensures that both types of resistors can meet the exact resistance values required, providing flexibility in design and manufacturing. Whether you're working with thick film or thin film resistors, the use of lasers for trimming is an innovative way to achieve unparalleled accuracy and performance.
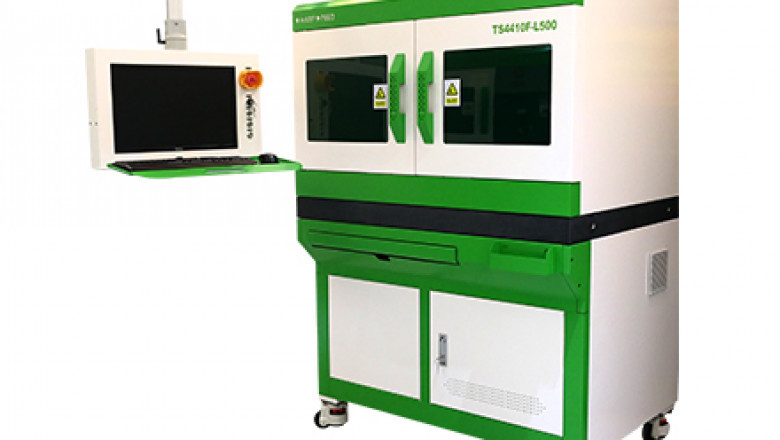

Comments
0 comment