views
The heart of smooth operations lies in structured work order management. It brings order to chaos by setting clear paths for task handling—from initial reporting through to final checks—ensuring teams remain on track, issues are swiftly resolved, and service levels remain high.
Key Components of an Effective Work Order System
An adaptable work order system should cover the entire lifecycle of a maintenance request.
1. Creation and Categorization
Every maintenance or service task begins with a clear, standardized work order. Categorizing the request—such as corrective maintenance, preventive maintenance, or inspection—ensures that it follows the appropriate workflow and is routed to the right team or technician.
2. Approval and Dispatch
Once a work order is created, many organizations enforce an approval step to verify scope, budget, and priority. After approval, dispatching the order to field technicians or internal teams involves assigning resources, defining deadlines, and specifying required parts or tools.
3. Tracking and Execution
Real‑time tracking—often via mobile devices—allows technicians to receive updates, report progress, and capture labor or material usage directly in the system. This visibility helps managers monitor status, identify bottlenecks, and reallocate resources as needed.
4. Completion and Analysis
After task completion, technicians log outcomes, upload photos or reports, and mark the order closed. Post‑completion analysis—examining resolution times, cost variances, and repeat failures—provides insights for continuous process improvement and more accurate future forecasting.
Benefits of Robust Work Order Management
Reduced Downtime
By automating scheduling and prioritizing urgent tasks, organizations can address equipment failures faster, minimizing unplanned downtime and production losses.
Improved Resource Utilization
Centralized visibility into labor availability, tool inventories, and spare‑parts levels ensures efficient deployment of personnel and materials, reducing idle time and overstocking.
Enhanced Compliance and Safety
A digital audit trail for every work order—complete with approvals, risk assessments, and safety checklists—helps maintain regulatory compliance and fosters a safer working environment.
Data‑Driven Decision Making
Advanced analytics on work‑order histories and KPIs enable predictive maintenance scheduling, trend analysis, and budget forecasting, empowering managers to make informed strategic decisions.
Best Practices for Streamlining Work Orders
Standardize Operating Procedures (SOPs)
Develop clear SOPs for each work‑order category. Train staff to follow these guidelines consistently, and update procedures regularly based on operational learnings.
Leverage Mobile Technology
Equip technicians with mobile apps that allow on‑site data capture, real‑time updates, and photo documentation. Mobile work order systems accelerate communication and reduce paperwork errors.
Implement Preventive Maintenance
Shift from reactive to preventive maintenance by scheduling regular inspections and servicing based on asset usage or condition metrics. Preventive strategies extend equipment life and reduce emergency repairs.
Prioritize and Categorize
Use a tiered priority system (e.g., critical, high, medium, low) to ensure the most urgent tasks receive immediate attention. Categorization by asset type or location further refines assignment and resource planning.
Foster Real‑Time Communication
Integrate messaging and alert features within your work‑order platform so that technicians, managers, and requesters stay aligned on progress, delays, and changes.
Choosing the Right Work Order Management Software
When evaluating digital work order solutions or CMMS work order management platforms, consider:
- Scalability: Can the system grow with your operation and handle increased order volumes?
- Integration: Does it seamlessly connect with ERP, inventory, and IoT monitoring tools?
- User Experience: Is the interface intuitive for both office staff and field technicians?
- Analytics: Are robust reporting and dashboard capabilities included for KPIs like MTTR, MTBF, and backlog?
- Mobile Access: Does the software offer offline mobile functionality for remote or low‑connectivity environments?
Implementation Tips
- Pilot Phase: Start with a single department or asset class to validate processes and gather user feedback.
- Data Migration: Cleanse and standardize existing asset, parts, and historical work order data before importing into the new system.
- Change Management: Communicate benefits clearly to all stakeholders and provide hands‑on training sessions.
- Continuous Improvement: Establish regular review cycles to refine workflows, update SOPs, and adjust system settings based on operational insights.
Frequently Asked Questions
1. What types of work orders are commonly used?
Corrective maintenance orders (urgent repairs), preventive maintenance orders (scheduled inspections), and inspection or audit orders (compliance checks).
2. How does mobile work order management improve efficiency?
Mobile access enables real‑time updates, reduces paperwork, and ensures technicians have up‑to‑date instructions and parts information on the go.
3. Can work order management software integrate with existing ERP systems?
Yes. Leading solutions offer open APIs and prebuilt connectors to synchronize data with ERP, inventory, and asset‑management platforms.
4. What KPIs should I track in work order management?
Key metrics include Mean Time to Repair (MTTR), Mean Time Between Failures (MTBF), backlog size, first‑time fix rate, and maintenance cost per work order.
5. How do I transition from manual to digital work order processes?
Begin with a pilot implementation, migrate and clean existing data, train staff on new workflows, and iterate based on user feedback and performance data.
Ready to streamline your maintenance operations?
Discover how ToolkitX’s Work Order Management solution can centralize requests, automate scheduling, and deliver actionable insights.
Learn more and start your free demo today »
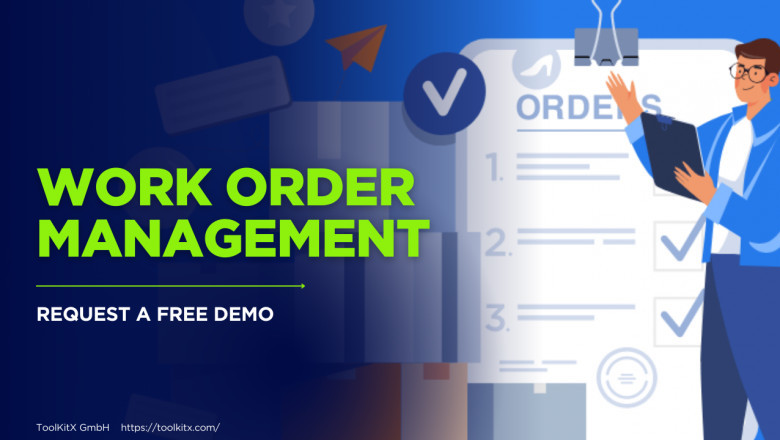

Comments
0 comment